How to make a grab bucket
Release time:
2012-01-10
How to make a grab bucket, and how to do it well? To do a good job with a grab bucket, you first need to understand what a grab bucket is, how grab buckets are classified, and what the structures of different types of grab buckets are.
How to make a grab bucket, and how can we do it well? To do a good job with a grab bucket, you first need to understand what a grab bucket is, how grab buckets are classified, and the structure of different types of grab buckets.
What is a grab bucket?
A grab bucket is a specialized tool used by cranes to grab bulk materials. It consists of two or more movable jaw plates that form a container space. During loading, the jaw plates close around the material pile, capturing the material in the container space. During unloading, the jaw plates open while suspended above the material pile, allowing the material to fall back onto the pile. The opening and closing of the jaw plates are generally controlled by the crane's lifting mechanism and wire rope.
How are grab buckets classified?
Grab buckets can be divided into two main categories based on their driving method: hydraulic grab buckets and mechanical grab buckets.
Hydraulic grab buckets are equipped with an opening and closing mechanism, typically driven by hydraulic cylinders. Hydraulic grab buckets, which consist of multiple jaw plates, are also known as hydraulic claws. They are commonly used in hydraulic specialized equipment.
Mechanical grab buckets do not have an opening and closing mechanism and are usually driven by external forces such as ropes or linkages. Depending on the operator's characteristics, they can be classified into double rope grab buckets and single rope grab buckets, with double rope grab buckets being the most commonly used.
Double rope grab buckets have a counter rope and an opening and closing rope, which are wound around the respective drums. Double rope grab buckets are reliable in operation, easy for operators, and have high productivity, making them widely applicable. When using two sets of double ropes, they become four rope grab buckets, and the working process is the same as that of double rope grab buckets.
Single rope grab buckets use the same wire rope for both the counter rope and the opening and closing rope. A locking device allows the wire rope to alternately perform the functions of countering and opening/closing. Single rope grab buckets are simpler in design but have lower productivity and are rarely used in large container operations.
Structure of the grab bucket
1. Lifting mechanism
The lifting mechanism adopts a standard structural layout, with the motor driving the drum through a reducer. The motor and reducer are connected by a gear coupling and drive shaft, making the structure compact and easy to assemble and maintain.
At the start of work, the supporting wire rope lifts the grab bucket to the appropriate position, then lowers it and opens and closes the wire rope. At this point, the weight of the lower crossbeam forces the main shaft of the bucket to open. When the collision blocks of the two ear plates of the bucket collide, the bucket opens. During the opening process, the distance between the upper and lower beam pulleys increases, then the supporting wire rope lowers, allowing the opened grab bucket to fall onto the loose pile of material. When the opening and closing wire rope is retracted, the distance between the upper and lower beam pulleys returns to its original position, completing the material grabbing process. The lifting and opening/closing wire rope is then lifted, and the entire grab bucket is hoisted and moved to the unloading area by the crane.
The lifting and opening/closing mechanisms of the grab bucket are driven by two motors, using different operational combinations to complete the complex actions of opening, closing, lifting, and lowering the grab bucket. Both motors can run in the same direction to lift or lower the grab bucket, while operating one motor or running both motors in reverse can open or close the grab bucket. Two main controllers are used to control the lifting and opening/closing motors separately, ensuring convenient individual or simultaneous operation. The main controller has positions of 1-0-1, and the rotor resistance of the controlled motors is automatically cut off by a delay relay-controlled acceleration contactor. The opening and closing direction of the grab bucket follows the direction of the crane's movement.
The motor used is a YZR motor for metallurgical cranes. This series of motors has a high overload capacity and mechanical strength. Its standard working mode is intermittent periodic working mode S3, with a duty cycle of JC40%. The insulation grade is F.
The reducer is a special cylindrical gear reducer for cranes, with a large load capacity and long service life. It can meet the requirements of frequent forward and reverse operation of the crane.
The brake actuator uses the Ed actuator produced with technology from Germany's EMG company, featuring a high operating frequency. The casing is made of cast aluminum alloy, and the motor has a non-oil-immersed structure with F-grade insulation. The transmission part has a double-sealed structure, ensuring reliable sealing. The lifting mechanism uses dual brakes, with a braking coefficient greater than 1.75.
The drums are of a double drum type, made of HT200 material. When lifting, the wire rope has three fixed circles and at least two circles on the drum.
Using Warrington-type wire ropes. They have low contact stress, long service life, and are easy to replace.
2. Running mechanism
The trolley running mechanism is driven by a motor fixed at both ends of the walking platform through a vertical reducer, which drives the wheels on both sides. The motor and reducer are connected by a full-tooth coupling, and the reducer and wheels are connected by a half-tooth coupling and drive shaft.
The motor used is a YZR motor for lifting and metallurgy. This series of motors has a high overload capacity and mechanical strength. Its standard working mode is intermittent periodic working mode S3, with a duty cycle of JC40%. The insulation grade is F.
The reducer is a special cylindrical gear reducer for cranes, with medium-hard tooth surfaces, large load capacity, and long service life. It can meet the requirements of frequent forward and reverse operation of the crane.
The design of the trolley frame and main beam can meet the dynamic load impact requirements when the trolley collides with the buffer at full speed.
The trolley wheels are made of ZG340-640 cast steel. The wheels undergo heat treatment, resulting in a hardness of HB323-380 on the tread and inner side of the wheel rim, with a hardened layer of at least 20mm and a hardness of 260HB at a depth of 20mm.
The crane and trolley running mechanisms use double push rod hydraulic brakes. They are reliable in braking and easy to maintain.
The main running mechanism is driven by motors fixed at both ends of the walking platform through reducers, which drive the wheel sets. The motors and reducers are connected by gear couplings and drive shafts, while the reducers and wheels are connected by full-tooth couplings.
Key words:
Next Page
Nantong Yukuang Machinery Equipment Co., Ltd.
Address: No.31, Huaxing Road, Jiuhua Town Industrial Park, Rugao City, Nantong City, Jiangsu Province
Telephone: 0086-513-85639998
Contact: Cao Yuli Tel: 0086-18662937010
Contact: Zhang Jie Tel: 0086-13815217243
E-mail: 965218109@qq.com
Access to related services
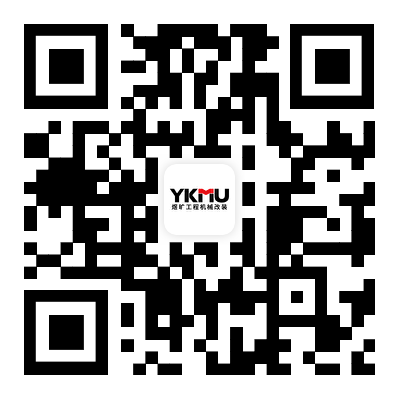
View mobile phone official website
Copyright©2025 Nantong Yukuang Machinery Equipment Co., Ltd. All Rights Reserved